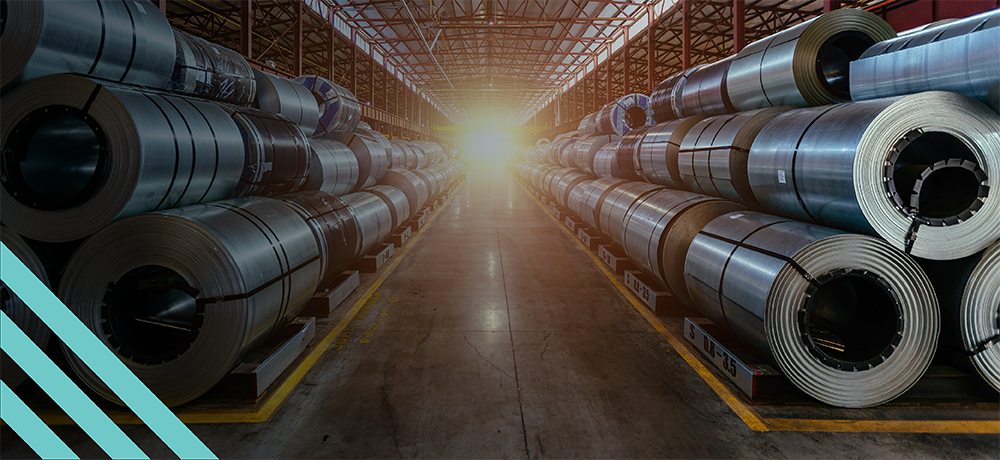
Businesses in construction, manufacturing and related trades are navigating a new reality: rising material costs.
Rising costs for materials such as lumber, steel, copper, and concrete, caused by inflation, supply chain disruptions, and global demand, are forcing companies to rethink how they plan, allocate and deploy their workforce.
This pressure is driving smarter, more strategic workplace planning, not only to manage budgets, but to adapt to an environment where every dollar and every worker is essential. For those willing to adapt, there is an opportunity to emerge stronger, more efficient and more resilient than ever before. Here’s a deeper look at how the industry is evolving its labor strategies to keep projects moving forward.
From Full-Time Crews to Flexible Skilled Trades Experts
One of the most noticeable shifts is the move toward more flexible, project-based labor. Rather than maintaining full-time crews on standby during material delays or budget strains, many contractors are turning to skilled trades staffing support.
This approach helps minimize downtime, cut unnecessary labor costs and ensure the right skills are available when needed. Whether it’s framing carpenters during structural work or licensed electricians for later phases, this strategy allows for adjustments in workforce size based on the stage of construction and the availability of materials.
Expert Skilled Labor Reduces Risk and Material Waste
With material prices soaring, precision has never been more critical. Even small mistakes or rework can quickly add up to cost overruns. As a result, there is an emphasis on prioritizing experienced, highly skilled tradespeople for projects where accuracy and efficiency are critical.
Demand is increasing for proven professionals—journeymen, foremen, and specialized tradespeople—who bring craftsmanship, reliability and strong attention to detail to every job. Investing in this level of quality labor ultimately safeguards project budgets, especially when material costs are anything but predictable.
One way to attract and retain these high-performing workers is through loyalty programs. Loyalty initiatives recognize and reward tradespeople for their craftsmanship and reliability, encouraging a culture that celebrates quality work. This supportive environment encourages long-term commitment and pride in their work, ultimately enhancing productivity and helping to control costs.
Cross-trained Workers Enhance Workforce Impact and Team Efficiency
In today’s job market; contractors are increasingly seeking workers with a versatile skill set who can take on multiple tasks on a job site. For instance, carpenters with basic electrical skills or concrete laborers trained to operate machinery are in high demand. Multi-skilled tradespeople are highly valuable, as they can easily adapt to different roles and needs.
This type of flexibility is crucial for project managers aiming to keep projects moving forward, even when specific trades face delays or shortages. Reducing the reliance on multiple specialty teams, companies can enhance overall efficiency, streamline operations and avoid costly disruptions.
To meet the growing need for adaptable teams, workforce development efforts are expanding. More programs are beginning to offer training and certifications that help tradespeople build additional skills and support long-term career growth.
Coordinating Labor Based on Material Availability
Material shortages and delivery delays have become a standard challenge across the industry, prompting contractors to adopt a more flexible labor schedule.
Rather than fully ramping up the workforce at the start of a project and risking downtime while waiting for materials to arrive, contractors are embracing more flexible labor strategies that adjust to shifting supply conditions.
One approach gaining popularity is deploying labor in phases that align with material arrivals and key project milestones. This just-in-time labor model ensures that workers are on-site when they’re needed most, helping to maintain high productivity, reduce idle time and stay within budget.
Bridging Procurement and Labor Planning
One of the most significant changes in the industry is the growing collaboration between procurement and labor teams. Leaders in construction are now making staffing decisions based on the availability and expected delivery times of materials. This new approach demands improved forecasting, more precise planning and flexible staffing strategies that can quickly adapt when projects receive the green light.
As material costs and supply chain issues remain unstable, this enhanced coordination is crucial for maintaining agility and ensuring that projects stay on schedule.
Partner with PRST for flexible skilled trades staffing solutions
Rising material costs are no longer just a budgeting issue. They are transforming how construction projects are planned and carried out from start to finish. Contractors that implement more effective labor strategies, develop skilled teams and utilize flexible staffing models are not only remaining competitive but are also setting themselves up for long-term success.
At PRST, we specialize in connecting contractors with skilled trades professionals to meet rising demands. We help complete projects on time, within budget and with the necessary expertise to get the job done correctly.
Looking for tradespeople and skilled laborers—right when and where you need them?